Micro e nanotecnologia/Microtecnologia/Film sottili/Sputtering
Quando un solido è bombardato con atomi o ioni o molecole, se l'energia delle particelle incidenti è maggiore della energia di legame dei solidi (5 eV) gli atomi nel solido sono espulsi dalla superficie. Gli atomi espulsi vanno nella fase gassosa e il fenomeno viene chiamato sputtering (non esiste un termine italiano). Se però l'energia è molto più elevata (qualche keV) le particelle bombardanti penetrano in profondità e il processo diviene la impiantazione ionica. Se invece l'energia è minore di 5 eV gli atomi rimbalzano sulla superficie o rimangono sulla superficie e poi lentamente, specialmente se sono atomidi gas nobili, vengono desorbiti e tornano nella fase vapore.

Il bombardamento con gli elettroni non produce sputtering a meno che l'energia non sia di molte centinaia di eV a causa del fatto che il trasferimento di energia cinetica dagli elettroni, leggeri, agli atomi del bersaglio, di molti ordini di grandezza più pesanti, è molto inefficiente. Per bombardare la superficie gli ioni sono usati in quanto la loro energia cinetica può essere resa sufficientemente elevata mediante campi elettrici.
L'energia di soglia per il processo di sputtering è abbastanza indipendente dal materiale e dal gas bombardante, in quanto non è essenzialmente un processo a due corpi, ma chiaramente gli atomi vicini giocano un ruolo essenziale. Infatti si può avere sputtering anche quando gli ioni incidenti arrivano con incidenza normale alla superficie e il fenomeno si spiega con una variazione della quantità di moto maggiore di 90o dovuta agli atomi vicini. Processi a collisioni singole si hanno solo in caso di bombardamento obliquo della superficie.
La deposizione mediante sputtering è una tecnica di deposizione fisica di film sottili (nel testo si useranno degli inglesismi quali film sputterati o sputterare non esistendo parole italiane che ne siano una fedele traduzione). La tecnica consiste nel rimuovere materiale dal target, che è la sorgente, e da questa depositarlo sul substrato, ad esempio un wafer di silicio. Il resputtering è la rimozione del materiale deposto durante il processo di deposizione da parte degli ioni o degli atomi incidenti sul substrato. Gli atomi sputterati dal target hanno una grande distribuzione di energie da frazioni di eV fino a decine di eV. Gli atomi sputterati se la pressione è sufficientemente bassa possono andare in maniera in linea retta dal target urtando il substrato o la camera da vuoto, causando eventualmente resputtering. Notiamo che gli ioni sono minoritari rispetto agli atomi neutri, infatti tipicamente sono ionizzati solo una piccola frazione degli atomi dell'ordine dell'0.01%. A pressioni maggiori gli atomi collidono con gli atomi del gas che agiscono come un moderatore e si muovono in maniera diffusiva, raggiungendo il substrato o la camera da vuoto e condensandosi dopo avere fatto un cammino stocastico. Cambiando la pressione, durante il processo, si può andare da urti balistici di alta energia a moto termalizzato di bassa energia. Il gas utilizzato nello sputtering è in genere un gas inerte come l'Argon. Per un trasferimento efficiente della quantità di moto, il peso atomico del gas utilizzato dovrebbe essere simile al peso atomico del materiale del target, quindi per depositare mediante sputtering materiali leggeri è preferibile il Neon, mentre per materiali pesanti possono essere usati il Krypton o lo Xenon. In pratica, per motivi economici, viene comunemente usato l'Argon, che è di gran lunga più economico rispetto agli altri gas nobili.
Gas reattivi possono anche essere utilizzati per depositare composti. In questo caso il composto può essere formato o durante il tragitto o sul substrato a seconda dei parametri di processo. Il fatto che molti parametri determinano le caratteristiche del film depositato rendono il processo complesso, ma anche permettono agli esperti di crescere film di proprietà microstrutturali particolari.
Uso dello sputtering
[modifica | modifica sorgente]Lo sputtering è comunemente usato dall'industria dei semiconduttori per depositare film sottili di vari materiali quali Tungsteno, Alluminio, Titanio, Rame. In genere poiché la temperatura del substrato può mantenersi bassa è la tecnica ideale per realizzare contatti metallici nei dispositivi elettronici. Una altra applicazione importante sono gli strati antiriflettenti sulle lenti che vengono comunemente realizzate con tale tecnica. La metallizazione di contenitori in plastica anche viene realizzata in genere con tale tecnica. Nella fabbricazione di CD e DVD il metallo depositato, in genere Alluminio, è depositato mediante sputtering.
Le superfici degli hard disk sono costituite da Ossido di Cromo (CrOx) o altri materiali sempre cresciuti con la stessa tecnologia.
Paragone con altre tecniche di deposizione
[modifica | modifica sorgente]Un vantaggio importante della deposizione via sputtering è che anche materiali con punto di fusione molto elevato possono essere sputterati, cosa praticamente impossibile con evaporazione termica. Film sputterati hanno una composizione molto simile a quella della sorgente. La differenza eventuale è dovuta alla diversa diffusione dal target al bersaglio, in quanto i materiali più leggeri sono deflessi più facilmente dal gas, ma la eventuale differenza di composizione non cambia durante la deposizione.
Film sputterati hanno tipicamente una adesione molto migliore al substrato di film evaporati. Inoltre un target contiene una grande quantità di materiale e quindi molto raramente occorre rinnovare il materiale del target e questo permette di utilizzare la tecnica anche in vuoto molto spinto (UHV). Le sorgenti per lo sputtering non contengono parti calde (per evitare surriscaldamento i catodi sono tipicamente raffreddate ad acqua) e sono compatibili con gas reattivi quali l'Ossigeno. Mentre l'evaporazione deve necessariamente essere effettuata dal basso verso l'alto, sputtering può essere effettuata anche dall'alto verso il basso, questo permette di evitare che polvere si depositi sui substrati nel processo di deposizione. Non esistono problemi di schizzi di materiale come avviene nell’evaporazione. Il processo di sputtering è compatibile con processi speciali quali la crescita epitassiale.
Gli svantaggi sono che il processo è più difficile da combinare con la tecnica di lift off usata per strutturare nel piano i film, questo a causa del fatto che il trasporto diffusivo, caratteristico dello sputtering, rende impossibile una ombra perfetta (cioè il film sputterato riesce a coprire anche zone nel cono d'ombra di evaporazione). In realtà, non potendo limitare completamente dove gli atomi vanno, si possono avere problemi di contaminazione. E' difficile controllare una crescita strato per strato. Inoltre nella matrice del film sputterato gli atomi dei gas inerti usati per il plasma sono inglobati nella struttura e costituiscono delle imperfezioni. La velocità di deposizione è in genere limitata a meno di 200 nm/min.
Il fenomeno fisico dello Sputtering
[modifica | modifica sorgente]Lo sputtering è un fenomeno fisico nel quale ioni, solitamente Ar+, vengono accelerati per mezzo di un gradiente di potenziale in modo da bombardare un “bersaglio” (Target), o catodo. Poiché gli ioni cedono la loro quantità di moto agli atomi posti sulla superficie del bersaglio, questi ultimi diventano volatili e sono trasportati sotto forma di vapore sul substrato dove vengono deposti sotto forma di film metallico.

- Si immette nella camera l’Argon che è un gas inerte. Fornendo una differenza di potenziale, gli “elettroni liberi” verranno accelerati lontano dalla carica negativa del catodo. Essi incontreranno nel loro percorso gli atomi di Argon e dall’urto riusciranno a ionizzarli, estraendo un elettrone che urterà un altro atomo di Argon e, per un processo a catena, si creerà il plasma . La diseccitazione degli atomi che non sono stati ionizzati, ma eccitati, determina la luminosità della scarica.
- Gli ioni Ar+ caricati positivamente vengono accelerati verso il catodo negativo (dove c’è il target) formando una corrente di plasma con una quantità di moto sufficiente da estrarre atomi dal materiale bersaglio (atomi non ionizzati, frammenti di molecole, ecc …) che si diffonderà in tutta la camera e, quindi, anche sul substrato.

- Gli atomi espulsi collidono con il substrato formando un film estremamente sottile. In genere la formazione del film consiste in cinque processi successivi di trasporto del materiale (precursore) sulla superficie, assorbimento dei precursori, diffusione di superficie, nucleazione e crescita di isole, crescita del film continuo. A volte può succedere che la quantità di moto dei precursori sia talmente grande da fare in modo che questi vengano impiantati nel substrato. La velocità di deposizione dipende dalla distanza del Target dal substrato.
lo sputtering è dovuto al trasferimento della quantità di moto dalla particella incidente all’atomo del bersaglio solido. per fare in modo che questo trasferimento sia significativo, bisogna che la particella incidente abbia almeno una massa comparabile con quella dell’atomo del bersaglio . Quindi gli ioni sono facilmente accelerati verso il bersaglio da un campo elettrico generato dalla differenza di potenziale applicata agli elettrodi e un certo numero N di atomi viene emesso dal bersaglio. Il numero N di atomi per unità di area che lasciano il substrato è:
Dove è la densità (unidimensionale) di corrente degli ioni che bombardano il catodo ed è proporzionale alla tensione applicata e alla quantità di Argon che immettiamo nella camera. q è la carica elettronica e Z è il numero di cariche per ione. è un parametro quantitativo che indica il numero di atomi estratti dalla superficie del target per ione che incide.

(adimensionale) (resa in inglese yield) è una funzione dell’energia posseduta dagli ioni, del peso atomico degli ioni e del peso atomico degli atomi del target. Altri contributi ad sono la dipendenza dall’energia di legame interatomico del target e dall’angolo di incidenza. Da considerazioni geometriche, è chiaro che l’incidenza obliqua degli ioni che colpiscono il bersaglio aumenta la resa dello sputtering. Con incidenza non perpendicolare è più facile che le collisioni conferiscano una componente di velocità diretta verso l’esterno del bersaglio agli atomi del bersaglio stesso. La curva di resa (yeld) dello Sputtering è una funzione dell’energia dello ione incidente. È all’incirca lineare fino ad una certa energia oltre la quale tende ad un asintoto orizzontale. A tali energie gli ioni penetrano così in profondità che l’energia non è più trasmessa agli strati superficiali ma a quelli sottostanti; in modo che gli atomi hanno probabilità nulle di uscire dal bersaglio. Questo è il principio di funzionamento di un altro processo: Impiantazione Ionica.

Bisogna però considerare che N è un numero medio, perché non tutti gli ioni che impattano fanno uscire un atomo dal target. Solo gli atomi degli strati superiori riescono a guadagnare energia sufficiente per essere emessi. A parte lo sputtering, lo ione incidente causa lo spostamento degli atomi ed alcuni ioni vengono addirittura impiantati nel bersaglio. Questi ioni impiantati possono venire in seguito emessi dal campione come atomi sputterati e addirittura andare a finire sul substrato. Alcuni ioni addirittura vengono riflessi dal campione senza far avvenire lo sputtering (processo alla base della Spettroscopia ad impatto da Ioni) ed altri ioni ,invece, nell’urto possono acquistare un elettrone e ricostituire un atomo di neutro. Anche elettroni possono essere espulsi dal target. Solo una piccola parte dell’energia dello ione è utilizzata per lo sputtering, la rimanente viene dissipata nello spostamento degli atomi all’interno del bersaglio, con il risultato di surriscaldarlo. Per questo motivo i target vengono raffreddati durante il processo. Se il sistema di raffreddamento non è sufficiente, l’aumento di temperatura potrebbe causare la fusione del target o del suo supporto!
Distribuzione angolare
[modifica | modifica sorgente]
b) Avvicinare il target al substrato non modifica sostanzialmente la distribuzione angolare.
c)nel caso si debbano riempire contatti stretti per diminuire ulteriormente la distribuzione angolare si fa uso di un collimatore interposto tra target e substrato.
Un difetto del processo di sputtering è la grande distribuzione angolare degli atomi che incidono sulla superficie, dovuta agli urti degli atomi provenienti dal target e il gas. Tale distribuzione angolare è un problema tecnologico quando si debbono metallizzare zone molto fonde e strette: in quanto il film via via crescendo tende a chiudere il buco superiore di fatto non permettendo un contatto tra lo strato superiore ed inferiore. La distribuzione angolare di un film tipico è mostrato nella figura a fianco (a). Avvicinando il target al substrato diminuisce la probabilità di urti, ma la distribuzione angolare non cambia in maniera apprezzabile, figura (b), in quanto la necessità di avere una buona uniformità di sputtering implica che vi sia una piccola separazione tra il target ed il substrato, riducendo gli urti con le molecole del gas. Anche in questo caso gli atomi incidono sulla superficie con un'ampia distribuzione angolare. Per diminuire la distribuzione angolare si può diminuire la pressione al di sotto di 0.1 Pa, generando un minor effetto di scattering del gas.
Nel caso in cui si debbano riempire stretti contatti, in alcuni casi si fa uso di un collimatore che restringe il flusso di atomi all'interno di un range angolare di +- 5° attorno alla normale come mostrato in figura (c).
Struttura e morfologia
[modifica | modifica sorgente]Studi approfonditi sulla struttura e la topografia di film sputterati metallici sono dovuti a J. A. Thornton [1]. In tale studio viene esteso il modello delle zone di crescita introdotto per i film evaporati[2]. Thornton introduce una nuova zona detta T, che è osservata per Argon a bassa pressione ed è caratterizzata da grani fibrosi densamente impacchettati. Il punto più importante di questa estensione del modello è l'enfasi che viene data alla pressione p che è considerato un parametro significativo per il processo. La ragione che la pressione gioca un ruolo significativo è dovuto al fatto che gli atomi che escono dal substrato escono con una elevata energia cinetica e la pressione attraverso il cammino libero medio determina l'energia con cui arrivano sulla superficie dove cresce il film. L'altro parametro che determina le prorietà del film è la temperatura di deposizione.
Poiché la deposizione attraverso sputtering viene inquadrata nelle crescite assistite da plasma, oltre agli atomi neutri vi sono anche specie cariche (come gli ioni Argon) che urtano la superficie dove viene cresciuto il film, e questa componente può esercitare effetti notevoli. Se definiamo i flussi ioni ed atomici con Ji e Ja, si trova che il rapporto Ji/Ja gioca un ruolo decisivo sulla morfologia e sulla struttura microscopica del film[3]. La ragione dipende da parametri strutturali quali le orientazione preferenziale dei cristalliti e dallo stato dello stress residuo.
Tipi di sistemi di sputtering
[modifica | modifica sorgente]dc Sputtering
[modifica | modifica sorgente]Il porta target funziona come catodo e il porta substrato come anodo. Quando si applica una elevata tensione in corrente continua (ad esempio 1000 V) al catodo, una scarica a bagliore (plasma) si innesca all’interno della camera mantenuta ad una pressione appropriata. Il plasma è normalmente costituito di ioni Ar+. Questa tecnica permette di evaporare solo film conduttori.
Una variante del processo consiste nell'utilizzo di un terzo elettrodo: un anodo, un target come in precedenza e di una ulteriore sorgente di elettroni. La camera viene mantenuta alla necessaria bassa pressione e gli elettroni vengono prodotti da una sorgente termoionica a filamento separata. Gli elettroni vengono accelerati verso l’anodo ionizzando in maniera consistente il gas. Questo processo viene chiamato scarica supportata da elettroni, perché avviene in presenza di una notevole quantità di elettroni generati dal filamento caldo che assicurano una elevata ionizzazione del plasma . Lo scopo del filamento caldo è di aumentare il numero di ioni che bombardano il target e di mantenerne costante il valore di polarizzazione. Il risultato è un aumento della velocità di deposizione rispetto al sistema a diodo planare ed un migliore controllo dei parametri di processo. Bisogna aggiungere che il filamento caldo rappresenta spesso un elemento critico che rende più frequenti gli interventi di manutenzione e la contaminazione dei film.
dc Sputtering Magnetron
[modifica | modifica sorgente]
Una variante del processo è il dc Sputtering Magnetron. Utilizza una sorgente in corrente continua per attivare il plasma e per creare una corrente di ioni che bombardano il bersaglio. Esso rende più efficiente lo sputtering in quanto intrappola in un campo magnetico, in prossimità del campione, gli elettroni secondari emessi dal target e li utilizza per ionizzare il gas inerte della scarica generando una corrente di ioni in prossimità della superficie aumentando la resa del processo. Quando una tensione negativa viene applicata al catodo gli elettroni emessi dal campione (oltre a quelli naturalmente presenti nella camera) vengono accelerati lontani dal target. Come la loro velocità aumenta, essi sono forzati a percorrere un percorso circolare dalla forza di Lorentz creata dal campo magnetico dovuto al magnete che è parallelo alla superficie del target. Gli elettroni sono così intrappolati in questo percorso finché non perdono la loro energia, cioè finché subiscono un urto con un atomo del gas, a questo punto vengono nuovamente accelerati e solo raramente vengono spinti lungo le linee del campo magnetico (quindi non più soggetti alla forza di Lorentz). Gli elettroni possono perdere la loro energia anche in altri modi per esempio eccitando atomi di gas Argon o diseccitandoli; fenomeno responsabile proprio della scarica luminosa. Il risultato di queste ripetute collisioni è la formazione di un'alta densità di ioni a poca distanza dalla superficie del target proprio nella zona della trappola magnetica. Il campo elettrico è perpendicolare alla superficie del target e accelera gli ioni dal plasma verso il bersaglio (poiché gli ioni hanno massa molto più grande di quella degli elettroni, essi risentono poco del campo magnetico); aumenta così la resa del processo di sputtering e si può notare dal fatto che il bersaglio viene consumato principalmente in quella zona. Inoltre, a pressioni di Argon di il cammino libero medio degli ioni corrisponde proprio alla distanza tra la zona magnetica e la superficie del campione.
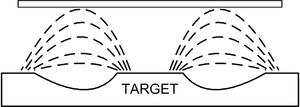
La densità di corrente al bersaglio non è uniforme, a causa proprio della forma del campo magnetico. La più grande densità di corrente la si ha dove il campo magnetico è parallelo al target, poiché gli elettroni riescono a seguire le linee di campo mentre si allontanano dal target; mentre gli elettroni che vengono emessi dalla superficie nella zona dove le linee di campo sono quasi ortogonali alla superficie, non sono intrappolati ma vengono accelerati. A causa di questa non uniformità della densità di corrente, abbiamo che la curva caratteristica corrente - tensione è simile a quella di un diodo e per questo viene chiamato Diodo Sputtering. La disuniformità della densità di corrente condiziona anche la distribuzione angolare degli atomi emessi dal bersaglio; si ha un andamento approssimativamente dato da una distribuzione cosθ rispetto alla normale alla superficie del target.
Sputtering a radiofrequenza (rf)
[modifica | modifica sorgente]Lo sputtering in dc è usato per depositare solo film metallici le cui superfici non siano fortemente ossidate. La ragione dello sviluppo della tecnica a radiofrequenza per la deposizione di film dielettrici e metallici risiede quindi nella maggiore flessibilità. Anche se per alcuni processi di deposizione di metalli la tecnica di sputtering in dc presenta caratteristiche peculiari di migliore controllo dei parametri di processo. Una superficie isolante nel plasma si carica negativamente rispetto al potenziale del plasma. Questo avviene perché la velocità degli elettroni liberi è molto maggiore di quella degli ioni del plasma. Con la rf è possibile aumentare la carica negativa del target. Applicando un potenziale AC ad un elettrodo in plasma si estrae una maggior corrente elettronica che ionica che agisce perciò come un raddrizzatore.
L’uso della RF permette di mantenere il plasma senza ricorrere all’emissione termoionica. L'efficienza del processo dipende dalla frequenza, a frequenze troppo basse (decine di kHz) la differenza di comportamento degli ioni e degli elettroni non è importante, quindi bisogna aumentare di molto la tensione del campo per fare avvenire la scarica a plasma. A frequenza di qualche MHz gli ioni non riescono più a seguire la variazione del campo elettrico e il processo di sputtering a rf diventa più efficiente. La scelta di operare a 13,56 MHz inoltre è stata dettata dall'autorità delle telecomunicazioni per non interferire con canali di telecomunicazioni.
I vantaggi dell’uso di un plasma in rf rispetto ad plasma in dc sono la possibilità di operare a pressioni relativamente basse del gas, che riducono le inclusioni di impurità e la non riproducibilità del film. Non è necessario usare un terzo elettrodo (filamento caldo d’emissione di elettroni). Si evitano perciò contaminazioni da filamento e la sua eventuale rottura.
Oltre ai metalli in rf si depositano pure leghe e composti senza modifiche nella composizione. Mediante sputtering reattivo possono essere depositati ossidi, nitruri, solfuri ecc.
Ion-beam sputtering
[modifica | modifica sorgente]
L'Ion-beam sputtering (IBS) è un sistema in cui il target è esterno alla sorgente di ioni. In genere gli ioni sono generati da elettroni confinati in una regione in cui è presente un forte campo magnetico. Quindi gli ioni sono accelerati dal campo elettrico verso una griglia in direzione del bersaglio. Un secondo filamento esterno neutralizza la carica degli ioni. Il vantaggio dell'IBS è che l'energia e il flusso degli ioni sono controllati in maniera indipendente. Poiché il flusso che colpisce il bersaglio è fatto di atomi neutri, possono essere sputterati con questa tecnica sia materiali isolanti che conduttori. Questa tecnica trova applicazione nella fabbricazione di dispositivi di piccola dimensione quali le testine degli hard disk. Viene in generato creato volutamente un gradiente di pressione tra la sorgente di ioni e la camera dove è posto il campione: cioè creando una sovrappressione nella camera della sorgente rispetto alla camera da vuoto e estraendo il gas nella camera da vuoto. Con una tecnica di questo genere si riducono le contaminazione e dà la possibilità di lavorare in Ultra Alto Vuoto (UHV). La tecnica non si presta a depositare grandi superfici e inoltre richiede una continua manutenzione.
Sputtering reattivo
[modifica | modifica sorgente]Nello sputtering reattivo, il film depositato è formato dalla reazione chimica tra il materiale del target ed il gas introdotto nella camera da vuoto (una miscela di gas inerte e gas reattivo). Spesso ossidi e nitruri sono fabbricati utilizzando sputtering reattivo. La composizione del film può essere controllata variando la composizione della miscela di gas. La stechiometria del film è un importante parametro per ottimizzare proprietà funzionali quali lo stress nel Nitruro di Silicio (SiNx) o l'indice di rifrazione del SiOx. Mediante sputtering reattivo viene fabbricato l'ossido di stagno e indio che è trasparente e conduttore, usato in optoelettronica e in particolare nelle celle solari.
Note
[modifica | modifica sorgente]- ↑ J.A. Thornton, Influence of apparatus geometry and deposition conditions on the structure and topography of thick sputtered coatings, J. Vac. Sci. Tech., 11,666 (1974)
- ↑ B. A. Movchan and A. V. Demchishin, Study of the structure and properties of thick vacuum condensates of nickel, titanium, tungsten, aluminium oxide and zirconium dioxide, Phys. Met. Metallogr., 28 83 (1969)
- ↑ H. Windischman,Intrinsic stress in sputter-deposited thin film, Rev. Sol. St. Mat. Sci., 17 547 (1992)
Altri Progetti
[modifica | modifica sorgente]Wikipedia contiene una voce su Sputtering (in italiano)
Wikipedia contiene una voce su Sputtering (in inglese)
Wikipedia contiene una voce su Sputter Deposition